Compact precision couplings for dynamic and precise handling and manipulation tasks

02.04.2025
Handling technology encompasses comprehensive process steps that serve to optimise a wide range of production processes. These include handling and assembly technology, automation and the entire field of automation and robotics. Due to the highest demands in terms of productivity and output, the systems operate highly dynamically in continuous or intermittent cycle operation using state-of-the-art servo technology. SCHMIDT-KUPPLUNG offers a wide range of different shaft couplings for this purpose - precise, with high torsional or axial rigidity and a lightweight design.
Perfect synchronisation of work processes in the fully automated assembly system
Joining, screwing, pressing, assembling or labelling - it's easy for modular, system-integrated rotary indexing machines that use indexing tables to handle these different operations with high productivity The workpieces to be processed are placed on the rotary indexing table using a fixture This pick-up then cycles from work station to work station accordingly In order to ensure that the workpieces are processed in large quantities, a precise and time-efficient process is essential This means that precise and highly dynamic drives are required for perfect synchronisation and control to the respective, usually pneumatically operated handling stations.
With its torsionally rigid and high-torque character, the compact Semiflex Dynamic shaft coupling is a perfectly coordinated integral component in the drive train Thanks to its slim and lightweight aluminium design, it supports the precise, highly dynamic work process.
Linear coupling for precise feed tasks in the highly productive gantry portal
Whether for high-precision contour machining in series part production or for palletising tasks in conveyor and storage technology or for the controlled joining process of metallic materials - electrically or pneumatically driven linear axes form the basis for dynamically operating handling and handling systems in these fully automated work processes.
They are usually modularly designed as multi-axis gantry portals in order to fulfil these tasks in a highly productive manner.
Such feed tasks are the speciality of the axially rigid linear coupling Loewe GK Linear. For example, the size Loewe GKL 27 cardan coupling has proven to be the ideal partner in dynamic traversing units in the drive train consisting of a linear motor and traversing carriage. In line with the high positioning accuracy and acceleration rates of the axes, the linear coupling made of aluminium has a high axial rigidity of 16,000 N/mm and extremely low mass inertia. It is available for maximum axial loads of up to 800 N and, as a compensating coupling, is also able to compensate for radial misalignments of up to 1 mm and angular misalignments of up to 3°.
Find out more about our compact precision couplings for demanding handling tasks - from automatic assembly machines and gantry systems to cobots and servo presses with extremely high thrust forces - in our "Handling technology" industry section.
Compact precision coupling for the high demands of fully automated thermoprocessing systems in the food industry

03.03.2025
Refining delicacies such as sausages or fish products to perfection - unthinkable without thermoprocessing systems. They ensure that we can find and enjoy the deliciously presented, smoked salmon at festive events or when visiting the hotel buffet in the morning, for example. Thanks to a considerable degree of automation, modern food production systems fulfil the high demands on the desired output in combination with optimum quality in terms of the sensory experience in terms of appearance and taste. The systems also offer flexible adaptation to the processing of different products.
The products to be processed pass through a wide variety of treatment processes in one system. The production stages are divided into heat treatment and cooling processes. This means that several thermally different processes such as drying, smoking, cooking, scalding, showering and cooling come together in the overall process.
The drive in such a fully automated system takes place outside the actual product area in a continuously operating process.
Due to the thermally different treatment stages, any tensions and displacements in the drive train must be absorbed by the shaft coupling to be used. Furthermore, quick and easy installation with the smallest possible dimensions is required.
Tasks made for the Semiflex Compact Plus precision coupling. In addition to compensating for axial and angular misalignments, it offers a high radial misalignment capacity combined with a compact design. Equipped with clamping hubs, the coupling offers the desired convenient and quick assembly and disassembly by fastening and loosening a radially operated screw.
For systems in the food industry with frequent cleaning processes or in accordance with the strict hygiene requirements for food processing machines, the compact coupling is available with a smooth, easy-to-clean, corrosion-resistant nickel coating or as a stainless steel version.
Find out more about our compact precision couplings for demanding packaging tasks in our "Packaging machines" industry section - from tubular and flat bag machines to fold wrapping and hygienic filling machines.
Precision coupling for compact, fully integrated beverage packaging system
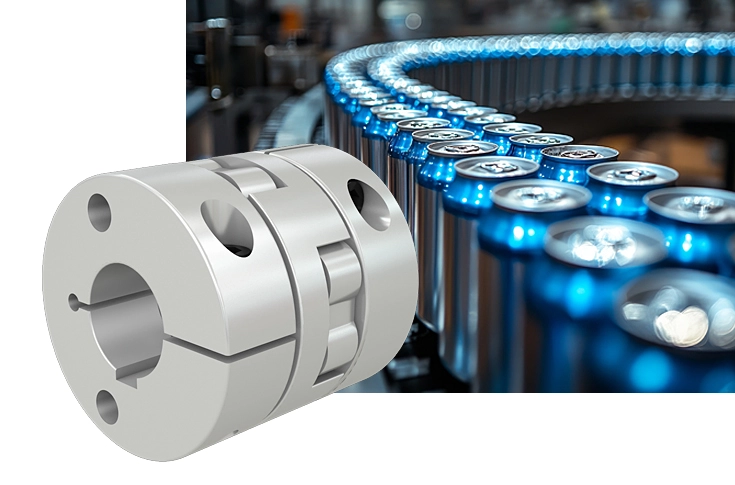
03.02.2025
Innovative, fully automatic packaging machines for beverages integrate the various process steps from feeding, filling and sealing the bottles or cans with the tasty and thirst-quenching refreshments through to labelling and palletising in sleeves, baskets or fully sealed packaging in a fully integrated overall system. Thanks to this dynamic technology, these systems achieve a high output with a small footprint.
In such packaging machines with extremely compact installation conditions, the torsionally rigid Semiflex precision coupling supports the synchronised sequence process to the individual processing stations. In the Compact Plus version, the all-metal coupling combines high torsional rigidity and torque capacity with a high displacement capacity in the slimmest design. In accordance with the strict hygiene requirements for food processing machines, the compact coupling has a smooth, easy-to-clean, corrosion-resistant nickel coating. The uniform and non-porous layer thickness created by chemical nickel plating offers excellent corrosion and wear resistance.
Find out more about our compact precision couplings for demanding packaging tasks in our "Packaging machines" industry section - from tubular and flat bag machines to fold wrapping and hygienic filling machines.
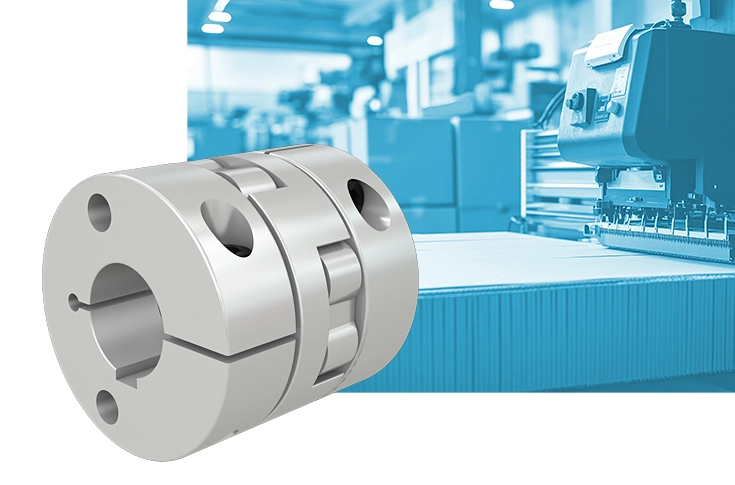
06.01.2025
"It must be coming slowly"...another check of the clock, the delivery company's app announced that the doorbell was about to ring. And then the doorbell rings. Hastily and eagerly we jump up and rush to the door - there he is, the delivery man dressed in the characteristic colours with the long-awaited parcel. We happily receive it and open the parcel, usually without a second thought, the outer packaging that protects our precious contents. We often forget that this parcel, made of corrugated cardboard, is the decisive factor in ensuring that we hold our ordered goods in our hands in pristine condition. But how is this protective and inherently stable outer packaging actually made?
The manufacturing process usually takes place on inline machines consisting of several sub-units. These produce the finished corrugated board packaging from sheets of cardboard. The sheet passes through the feeder, printing, creasing and slitting unit as well as the punching and folding station before being glued together in the folder gluer to form the finished package. In such packaging machines with extremely compact installation conditions, the torsionally rigid Semiflex precision coupling supports the synchronised sequence process to the individual processing stations. In the Compact Plus version, the all-metal coupling combines high torsional rigidity and torque capacity with a high displacement capacity in the slimmest design. The flange-mounted version ensures integration in the tightest of spaces in customised attachments (example size C 265, outer diameter 100 mm, overall length 88 mm, nominal torque 265 Nm, radial misalignment capacity of up to 8 mm).
Find out more about our compact precision couplings for demanding packaging tasks in our "Packaging machines" industry section - from tubular and flat bag machines to fold wrapping and hygienic filling machines.
Always a well-rounded thing!
Compact precision coupling supports the accurate cycle process in rotary transfer machines

02.12.2024
Joining, screwing, pressing, assembling or labelling - it's easy for modular, system-integrated rotary indexing machines that use indexing tables to handle these different operations with high productivity The workpieces to be processed are placed on the rotary indexing table using a fixture This pick-up then cycles from work station to work station accordingly In order to ensure that the workpieces are processed in large quantities, a precise and time-efficient process is essential This means that precise and highly dynamic drives are required for perfect synchronisation and control to the respective, usually pneumatically operated handling stations.
With its torsionally rigid and high-torque character, the compact Semiflex Dynamic shaft coupling is a perfectly coordinated integral component in the drive train Thanks to its slim and lightweight aluminium design, it supports the precise, highly dynamic work process
Find out more about our compact precision couplings for demanding handling tasks - from automatic assembly machines and gantry systems to cobots and servo presses with extremely high thrust forces - in our "Handling technology" industry section
Only the result counts here!
The shaft coupling must deliver: precision and dynamics are the order of the day in the testing process
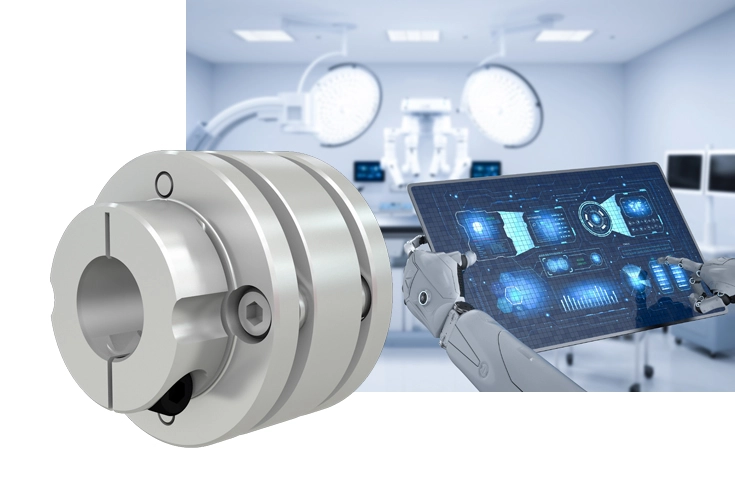
06.11.2024
Determining the mechanical and electrical performance characteristics of small, stepper or servo motors is essential in order to draw conclusions about the efficiency of the respective test specimen. Specialised universal test benches for electric motors that run at high speed put these controllable drives through their paces and provide precise, traceable and recorded measurement data. The focus here is on recording key figures such as torque, speed, voltage, friction torque and the effects on thermal results.
In order to determine the most accurate measurement results, the entire drivetrain in the test systems is trimmed for absolute accuracy and precision. In addition, the focus is also on pronounced dynamics for fast reaction times and acceleration rates.
This is where the Servoflex servo disc coupling with its torsionally rigid, high-torque and lightweight design proves to be a perfectly matched partner as an integral component in the drivetrain. Its pronounced power density coupled with a minimal mass moment of inertia guarantee high positioning accuracy and dynamics.
Find out more about our compact precision couplings for testing and measuring systems in our "Testing technology" industry section - from high-speed test benches to high-torque mixed-mode material test benches.
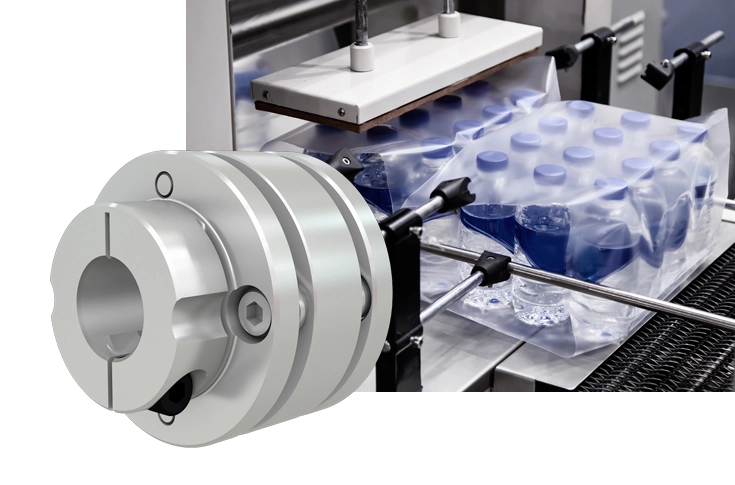
Wolfenbüttel, 07.10.2024
Modern packaging machines set standards in terms of speed combined with high precision for efficient, safe and highly productive packaging in the food and non-food sectors. SCHMIDT-KUPPLUNG torsionally-stiff shaft couplings deliver their performance in a wide variety of packaging machines and processes, scoring points with their precision, compactness and high radial displacement and offset capacity.
They are the perfect partner, for example, for driving cartoning modules, folding boxes and folding units, for thermoforming devices in thermoforming machines for the packaging industry, in filling systems for the accurate dosing of powdery or liquid media or in label printers that label products or packaged products with a high output rate. They also ensure the perfect process when grouping and filling loose products into saleable or transportable containers using fully automatic tray packers.
Find out more on our industry page "Precision couplings for packaging technology"
Always in perfect shape
Axially rigid linear coupling for powerful feed in fully automated cutting systems
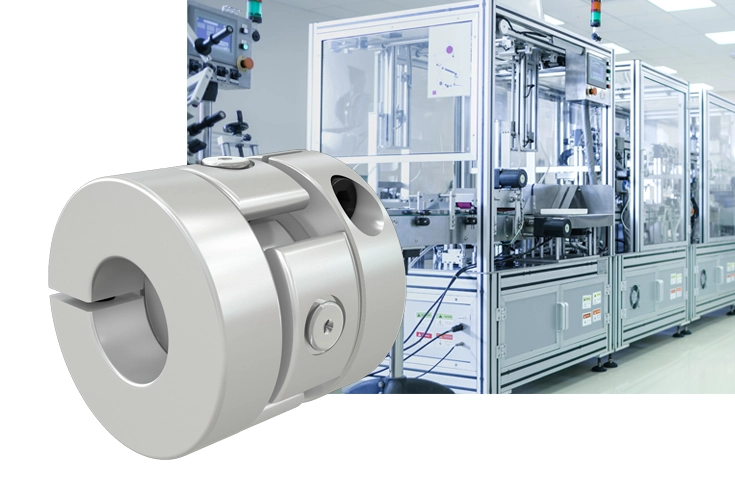
02.09.2024
Fully automatic cutting systems for processing aluminium raw panels, solid wood or plasterboard and fibreboard into customer-specific cuts, for example, are complex high-end system solutions consisting of a process-optimised combination of different sawing and cutting stations, transport and storage systems. Thanks to the automated work processes coupled with high feed speeds and flexibility, these systems ensure maximum productivity with perfect cutting quality of the shaped materials.
Linear coupling for powerful feed
Maximum axial rigidity and axial load - for the feed and infeed of the tool slide, the Loewe GK Linear cardan coupling has proven to be the perfect partner in such fully automated cutting systems. In accordance with the high positioning accuracy and feed force in these moulding machines, the linear coupling has a high axial rigidity of up to 61,500 N/mm and is available for maximum axial loads of up to 13,000 N. As a compensating coupling, it is also able to compensate for radial misalignments of up to 2.5 mm and angular misalignments of up to 3°.
Heavy loads made easy
If the requirements in terms of axial stiffness and feed force are even more pronounced, the design department at SCHMIDT-KUPPLUNG develops specially customised coupling solutions, for example for axial loads of up to 60.000 N and more.
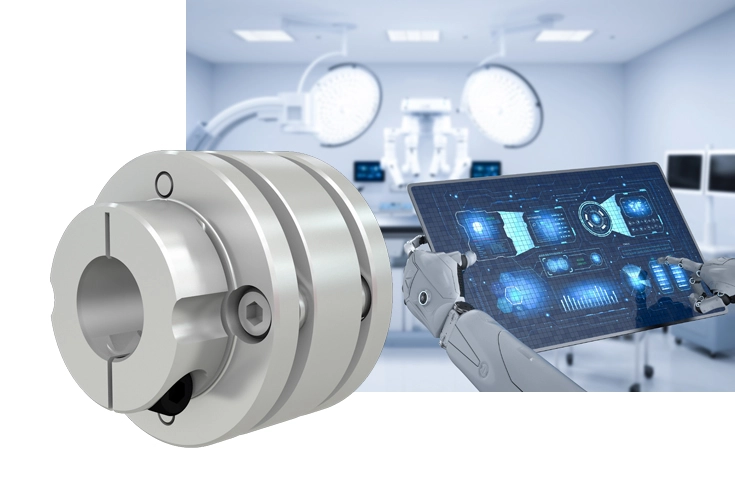
09.08.2024
Test devices for angle encoders enable the referencing of angle encoders such as resolvers etc. in high-precision measurements. For example, angle encoders of brushless EC DC motors can be compared with the respective rotary encoder of the test station on these test systems. The measured values are made available on analogue and digital output channels for subsequent precise evaluation by PC. This test procedure provides important results, as the motors, which operate with high acceleration and in high speed ranges, are used in conjunction with the angle encoders for precise positioning tasks.
This is where the lightweight aluminium Servoflex comes into play. The selected size of the servo disc coupling is equipped with offset clamping hubs on both sides and precisely meets the requirements in terms of high precision in accordance with the highly accurate measurement results to be achieved, the compensation of universal shaft misalignments as well as the minimised mass moment of inertia and working in a wide speed range.
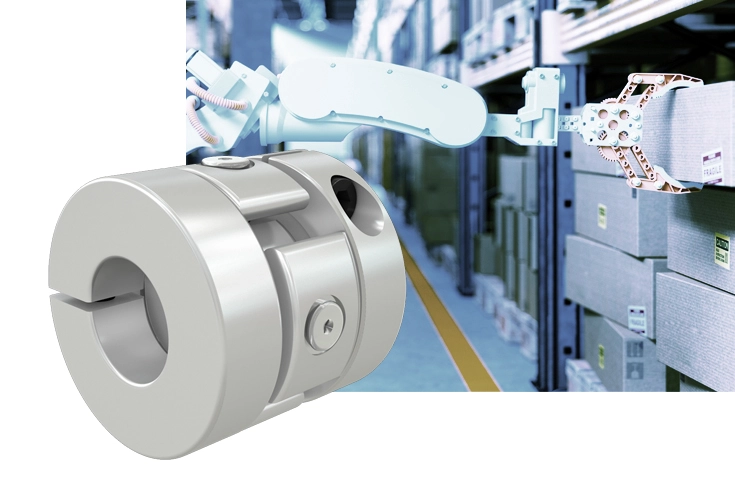
01.07.2024
Whether for high-precision contour machining in series part production or for palletising tasks in conveyor and storage technology or for the controlled joining process of metallic materials - electrically or pneumatically driven linear axes form the basis for dynamically operating handling and handling systems in these fully automated work processes.
They are usually modularly designed as multi-axis gantry portals in order to fulfil these tasks in a highly productive manner.
Such feed tasks are the speciality of the axially rigid linear coupling Loewe GK Linear. For example, the size Loewe GK L 27 cardan coupling has proven to be the ideal partner in dynamic traversing units in the drive train consisting of a linear motor and traversing carriage. In line with the high positioning accuracy and acceleration rates of the axes, the linear coupling made of aluminium has a high axial rigidity of 16,000 N/mm and extremely low mass. It is available for maximum axial loads of up to 800 N and, as a compensating coupling, is also able to compensate for radial misalignments of up to 1 mm and angular misalignments of up to 3°.
Versatile choice of connection
Internal thread, threaded studs, clamping hubs or a combination of these hub types - the linear coupling leaves nothing to be desired when it comes to the connection..
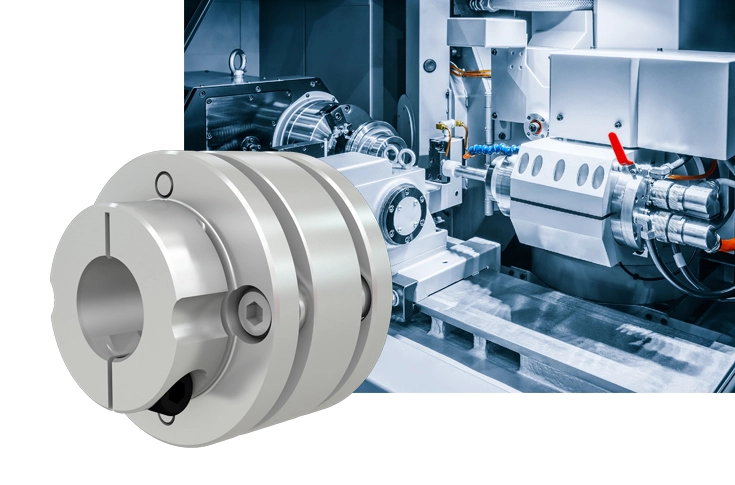
03.06.2024
In the pharmaceutical industry, in medical technology or in process engineering, they are used everywhere - high-precision dosing units.
In volumetric dosing systems for liquids, the material discharge is exclusively volume-based and therefore quantity-based. In most cases, these dosing systems are calibrated to the respective material in advance of a dosing process in order to guarantee an exactly defined dosing discharge per time unit. Process reliability and absolute accuracy and reproducibility are at the forefront of these semi-automatic and fully automatic dosing systems.
The light and precise Servoflex servo disc coupling shows its strengths in such dosing systems. Lightweight and minimised mass inertia combined with pronounced torsional rigidity and zero backlash - these are the features of the Servoflex and thus ensure coordinated interaction for automated, high-precision volume dispensing. The Servoflex SFC 090D double-cardanic version has a torsional rigidity of 50,000 Nm/rad and compensates for radial misalignments of up to 0.52 mm, axial misalignments of up to 1.3 mm and angular misalignments of up to 2°. It is available for speeds of up to 10,000 rpm.
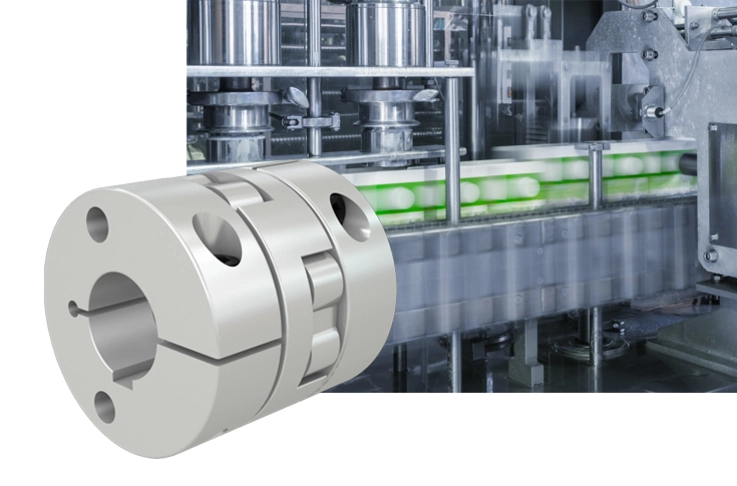
02.05.2024
There they are on the shelves, attracting our maximum attention – products packaged in visually appealing packaging. However, as we consumers always want to be on the safe side, purely functional factors also play a decisive role in addition to the sales-promoting aspects desired by the respective manufacturers. These include the shelf life of the packaging contents, as products are not used or consumed immediately. A positive best-before date signals freshness and the product's continued usability.
Fully automatic horizontal flow wrapping machines guarantee an absolutely durable and long-lasting presentation of packaged food or non-food products at the point of sale. These flowpack machines are modular and compact with a high output.
Various feed systems such as conveyor chains or infeed belts transport the products to be packaged to the travelling sealing units, which ensure that the bag is absolutely leak-proof by means of transverse and/or longitudinal sealing and thus ensure the shelf life of the products in the packaging itself.
Hand in hand for an optimum result
The slimline Semiflex C 70 precision coupling is the perfect partner for such compact tubular film machines.
Thanks to its high torsional rigidity and precision, it supports the high productivity and quality requirements of this fully automated packaging process. Despite its extremely compact length of just 59 mm, the all-metal coupling enables a high radial displacement capacity of up to 5 mm. The shafts are connected via clamping hubs or alternatively via clamping hubs in a half-shell design. The latter variant is the solution for radial mountability in limited installation conditions. The flange-mounted version is even shorter. Here, the torsionally stiff shaft coupling is connected directly to the customer-specific attachment parts.
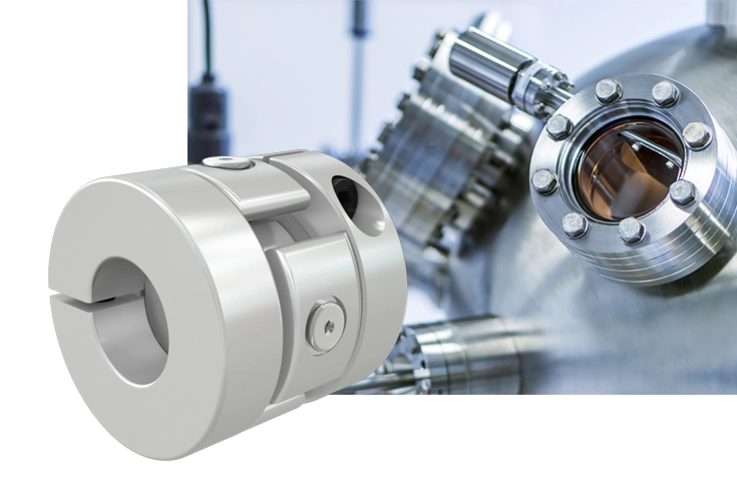
02.04.2024
Delicate, precise, elegant or fast - these are the attributes that flexible couplings in the medical and pharmaceutical industry must fulfil in order to manufacture medical technology products, diagnose them safely and gently or analyse samples accurately.

04.03.2024
In laboratory and process technology, in plant engineering or in coating systems, there is hardly an area where high-performance valves are not used. These electrically or electro-pneumatically actuated high-performance valves enable a fast and precise operating process and are used in countless areas of mechanical and plant engineering, for example to throttle or precisely distribute gas and liquid flows. Productivity optimisation plays a central role in these systems.
In high-performance valve systems controlled by electrically driven actuators, the Servoflex and Spinplus precision couplings are available as a coordinated partner and support these systems with their high torsional rigidity, compactness and minimised mass moment of inertia. A suitable connection to ensure that the valves operate with consistently high performance, precision and high repeatability when throttling, shutting off or dosing the respective flow rate.

05.02.2024
One of the strengths of the Semiflex precision coupling is its ability to compensate for high radial misalignments without taking up too much space - high performance in a compact design. The comprehensive range of standard couplings is available to compensate for this misalignment of up to 33 mm and covers a torque range of 40 to 14,500 Nm.
Thanks to its variability and modularity, the coupling is at home in a wide range of industries and applications. The range of applications extends from paper and laminating machines to plastics and packaging systems, profiling machines and automatic assembly machines.
However, it is not uncommon for customers to bring very special requirements to SCHMIDT-KUPPLUNG's design department. These include, for example, additional tensile and compressive forces in the drive train, vacuum conditions or special environmental conditions such as surfactants and organic acids caused by cleaning and processing operations in the food industry. Furthermore, seawater from offshore applications can be challenging for a coupling system. The answer to this is coupling solutions that are precisely customised to these tasks.
Seawater cannot harm it: Torsionally rigid coupling with high misalignment compensation in a space-saving design
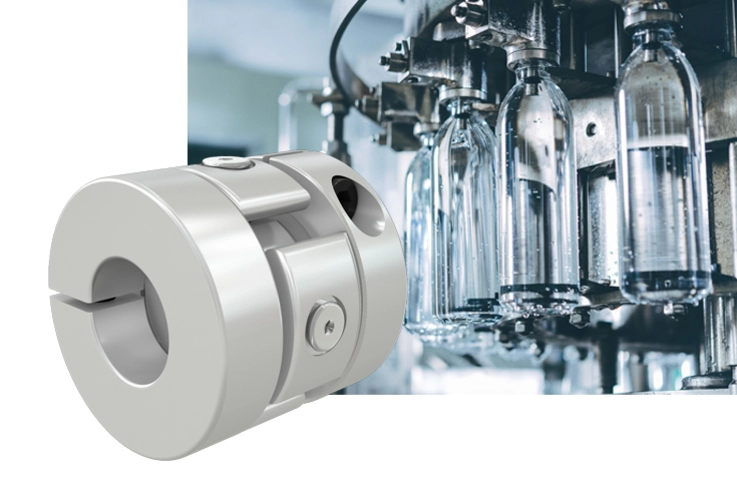
05.01.2024
Systems in the pharmaceutical, cosmetics or foodstuffs sectors require components whose materials are adapted to the most diverse conditions. Special hygiene aspects play a central role here. Furthermore, these systems are permanently cleaned and the components must withstand the cleaning agents or disinfectants used, which places special demands on the materials.
Hygienic regulations in food packaging plants or in plants of the food industry
Drive components in the food processing or packaging industry are subject to special requirements with regard to the materials they use.
Even though they are not in direct contact with media, the systems and components are subject to a permanent cleaning process with correspondingly special demands on the materials of the drive technology products. Depending on the level of corrosion stress, the materials 1.4301 and 1.4404, among others, have proven themselves as stainless steels in these industries.
Precisely dosed: Loewe GK Linear as an adapted partner for accurate filling quantities
To ensure that liquid or pasty products, for example, reach the supermarket shelves ready for sale, these products pass through various production stages in food dosing systems. Equipped with dynamically operating servo cylinders, these systems work with a highly productive output. The dosing process is of great importance, as the weight fluctuation of the product in the final packaging must be kept constant with only minimal tolerance throughout the entire production. Permanent product changes in the filling system make corresponding cleaning cycles necessary.
For the precise linear drive of the dosing station responsible for the filling quantity, the Loewe GK of the Linear series proves to be an adapted partner. In stainless steel design with matching plain bearings, it defies the permanent cleaning processes and does not allow itself to be upset by the common cleaning agents used in the process.
From A to B with pinpoint accuracy: with the Loewe GK Torque as if from a single mould in hygiene-critical material flow
A wide variety of conveyor systems are suitable for transporting bottles, cans or cartons in the food, cosmetics and pharmaceutical industries. These include, for example, sliding-belt, slat-band or link-chain conveyors. Thanks to their modular and flexible design, these conveyor systems connect filling and packaging lines with each other, among other things.
When designing these systems, great attention is paid to ease of cleaning. This applies to both optimum accessibility and careful material selection, in order to be perfectly equipped for the cyclical damp or wet cleaning processes.
In the drive train, the unit consisting of a corrosion-protected or mostly corrosion-resistant motor with the corresponding IP protection class and Loewe GK of the Torque series in stainless steel version forms a coordinated, hygiene-friendly drive solution.
The Servoflex delivers!
The servo disk coupling supports the high travel speed in the feeding and loading process
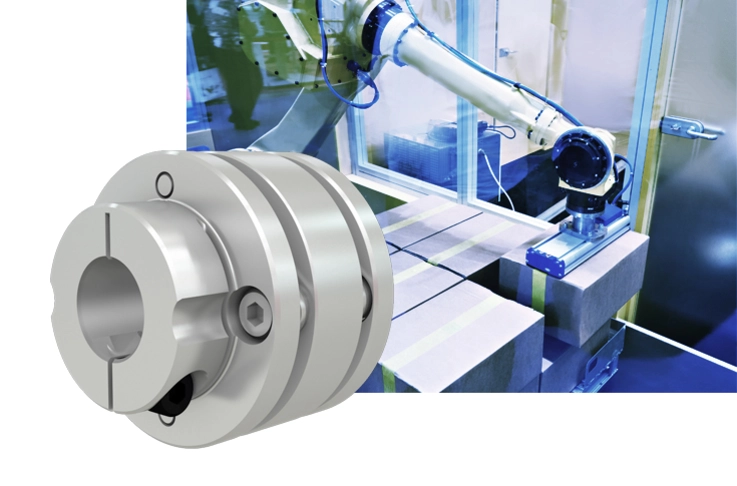
01.12.2023
Who wouldn't want that in innovative machine and plant engineering? Time savings, increased productivity with associated set-up time optimization - loading robots are the friend and helper here. They ensure the automatic and intelligent loading and workpiece feeding of a wide variety of machines in no time at all - from systems in the food industry to CNC lathes and milling machines. The highly dynamic servo motor in each robot arm ensures high travel speeds during the feeding process. This is where the lightweight and precise Servoflex servo coupling comes into its own. Lightweight and minimized mass inertia combined with pronounced torsional rigidity and zero backlash - these are the features of the Servoflex and ensure coordinated interaction with the energy-efficient drive. The Servoflex SFC 060D double-cardanic version has a torsional rigidity of 35,000 Nm/rad and compensates for radial misalignments of up to 0.34 mm, axial misalignments of up to 0.9 mm and angular misalignments of up to 2°. It is available for speeds of up to 10,000 min-1.
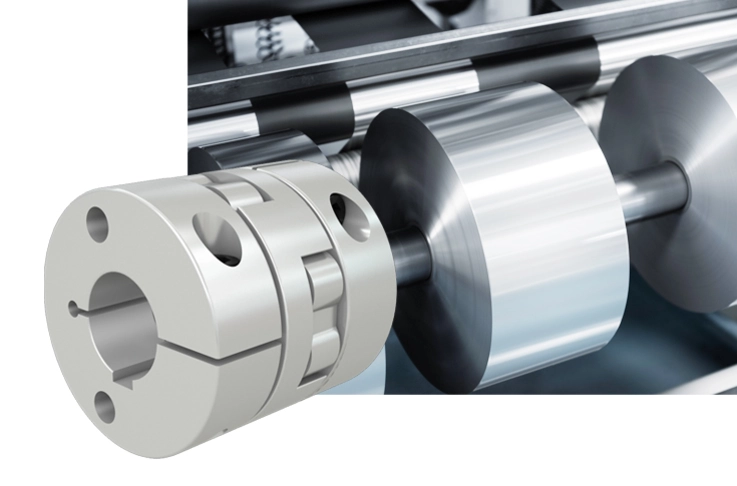
20.11.2023
Coating and laminating systems permanently bond different carrier materials with wafer-thin layers in order to provide them with the desired additional properties in a targeted manner. The systems work extremely precisely, because the substrate must be provided with the defined layer thickness in a highly accurate and uniform manner.
Matched couplings offer the corresponding technical properties and always work in angular synchronisation with a high degree of precision during variable adjustment movements of the coating rollers during operation.
Qualities are in demand: compactness and high misalignment possibilities with permanent synchronisation of the coupling are essential here
In addition to usually restrictive installation conditions, the corresponding coating rollers in such systems are adjusted by several millimetres during operation due to the processing of different materials and thicknesses.
A requirement profile made for the Semiflex. Compact, powerful and equipped with a high radial displacement capacity, it has these coating and laminating tasks safely under control.
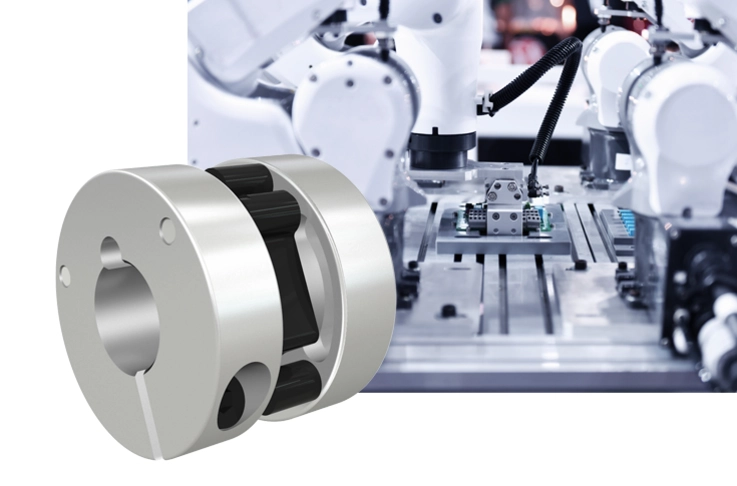
Wolfenbüttel, 09.10.2023
Bottles have been filled, bags have been packed - when it comes to the final, particularly tight-fitting, protective packaging of these end products - then wrap-around packers come into play. At the end of the process chain, these fully automated systems ensure an overall economically optimized manufacturing process. With maximum flexibility, they adapt to a wide variety of packaging designs and collect, group and pack the products in the blink of an eye into folding cartons, trays, display cartons or other cartons of different formats, depending on the choice made.
In the pick-and-place process, the Servoflex servo disc coupling supports the accurate positioning and filling of the packages with the respective products in a manner that is gentle on the product. Thanks to its low mass moment of inertia and high torsional stiffness, it is made for dynamic and extremely precise operation with high output.
Sensors and encoders are usually additionally used for positioning monitoring. The Controlflex encoder coupling ensures the exact and precise pickup and transmission of the measuring pulses.

Wolfenbüttel, 14.09.2023
Demanding transport tasks for hot, cold, corrosive or heavy materials usually require special transport solutions.
Plastic conveyors or conveyor belts made of rubber or textile materials often reach their limits here due to the ambient temperatures and/or conditions. Wire conveyor belts in a wide variety of shapes and individual designs meet these challenges.
In the production of these robust conveyor belts, hydraulic, pneumatic or electromechanical lifting cylinders work hand in hand with the actual bending mechanism in bending machines. The cardan coupling of the Loewe GK Linear series is an integral part of this drive unit. Due to its high axial rigidity in conjunction with its high radial and angular displacement capacity, the linear coupling ensures the precise transmission of the lifting forces to the forming, contouring tool heads while at the same time relieving the entire system of function-related tensions.
The individual, defined bent wire strands finally form a braid and, for example, as flat wire or round wire link belts, ensure reliable transport in a wide variety of applications and industries.
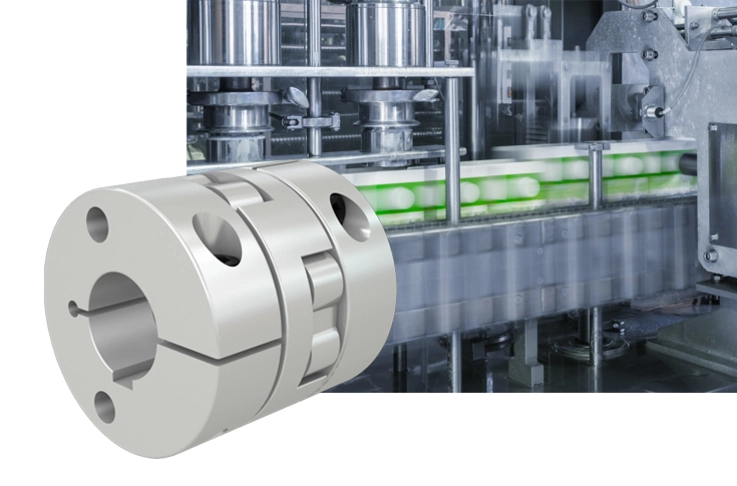
Wolfenbüttel, 01.09.2023
It is not only children's eyes that light up with these products – little chocolate bars or sweet wafers, perfectly presented on the supermarket shelves, are a joyful attraction. But before they get into our hands, are hastily unpacked and then cause sudden moments of happiness in the palate, they first have to be wrapped in an appropriate wrapping material. Fold wrapping machines take over this task fully automatically. Perfectly synchronised, the respective product and the corresponding packaging material pass through the individual stations from wrapping to accurate folding. The delicious product is ready, wrapped in high-quality and visually appealing packaging. Compact fold wrapping machines equipped with modern servo technology are extremely adaptable in terms of formats and packaging materials and operate in the highest performance range.
Hand in hand for an optimum result
The slim Semiflex C320 precision coupling is the perfect partner in such compact, high-performance packaging systems.
With its high torsional stiffness of 73.000 Nm/rad and its precision, it supports the high productivity demands when providing the sweets with inner and outer wrapping, including the precisely fitting folding process. The all-metal coupling offers the desired extremely compact design and also enables a high degree of radial misalignment compensation.
Learn more about the compact Semiflex
Further interesting information on precision couplings for packaging machines
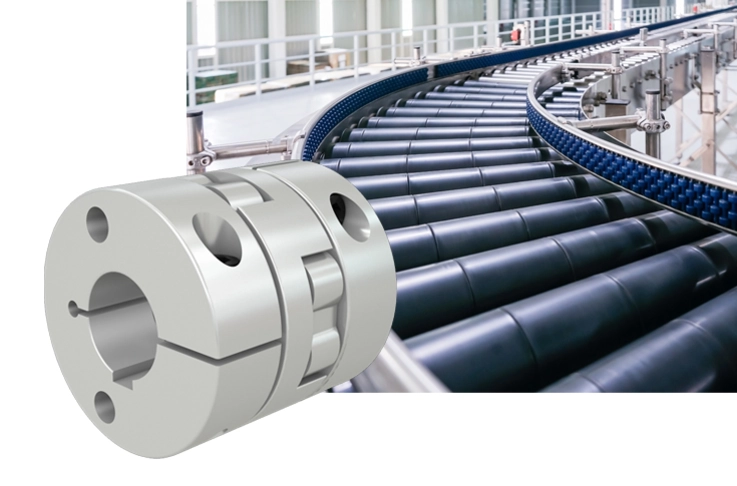
18.08.2023
Efficient material flow with its sub-areas of conveying and palletising technology is an important component in today's logistics for optimising internal material processes. Whether unit loads are conveyed from A to B on rollers or belts with pinpoint accuracy, whether small parts are stored and picked at breakneck speed, or whether palletising robots assemble and load packaged end products onto conveyor systems with high precision - for all these tasks, the coupling is of great importance for a precise and smooth process.
When it pushes and pulls
Loewe GK Linear as a precisely matched partner for high-performance reversing solenoids
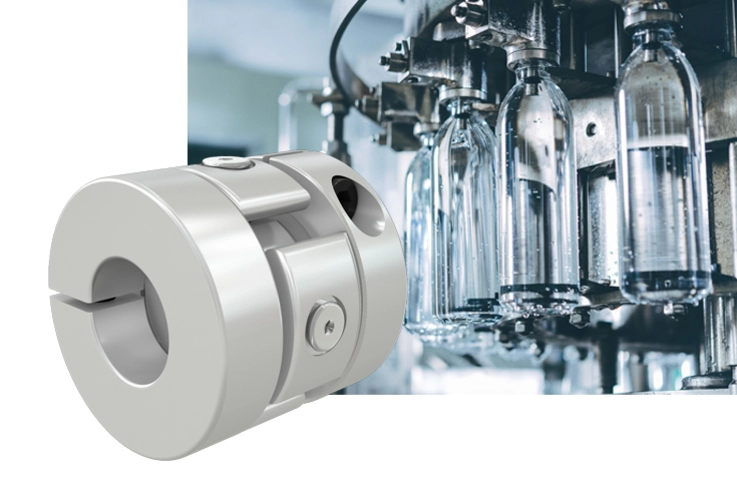
08.08.2023
DC high-performance reversing solenoids are popular systems when it comes to precise and dynamic positioning movements in linear drive concepts. The reversal of movement "pulling and pushing" in these compactly designed systems is achieved by the constructive design using two coils. This means that the regulation and control of the direction of movement is oriented to the respective supply voltage. Despite their compact design, the reversing solenoids combine large forces with relatively long stroke movements and offer a long service life even at high switching frequencies. These technical features make them sought-after linear systems in automation technology, the packaging industry and general mechanical engineering.
Precise transmission of linear forces at high frequency
As an integral component here, the Loewe GK series linear couplings fulfil the precise transmission of the linear forces of the high-performance actuators. On the one hand, the lightweight, aluminium linear couplings emphasise the high power density and dynamics of the magnet systems through their symbiosis of compact design and distinctive performance data. On the other hand, the range of coupling sizes allows them to be optimally matched to the different performance classes of the lifting systems. In addition, the wide range of connection options guarantees a perfect fit. Versions are available with internal threads - either regular or fine threads, with threaded pins, with clamping hubs or in a combination of the above-mentioned mounting options.
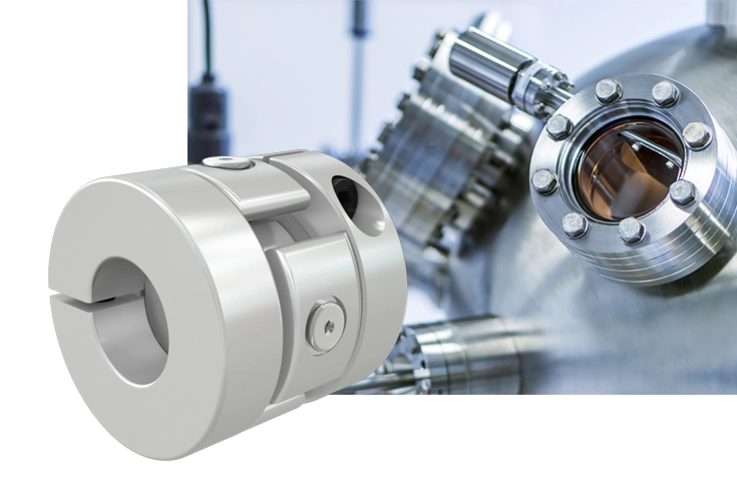
06.07.2023
Linear drive concepts do their job in countless areas of mechanical engineering and are, for example, a guarantee for dynamic positioning tasks or for the precise dosing of liquids or gases in pneumatically or hydraulically operated linear units, electromechanical actuators or in piston pumps.
As a coordinated integral component in these systems, axially stiff linear couplings are required here, which are responsible for the precise transmission of linear forces while at the same time relieving the machine components of tensions and damaging transverse forces.
This is exactly the job of the axially stiff Loewe GK Linear coupling: precise transmission of purely linear tensile and compressive forces with simultaneous compensation of radial and angular misalignments.
Precise metering with simultaneous system relief in piston metering pump
Whether in the pharmaceutical sector and in laboratory technology or in process engineering - piston metering pumps do their work everywhere and are an integral part of fully automatic work processes. Depending on the area of application, they meter liquid media in the millilitre range or convey liquids of up to more than a thousand litres per hour. Dosing pumps are usually oscillating displacement pumps. A precisely defined volume of liquid is soaked in during the return stroke of the displacer and pressed into the dosing line during the pressure stroke. The stroke-executing piston rod is driven either pneumatically, hydraulically or via a motor. In this application, the stroke-executing piston is driven via an axially acting air motor.
The Loewe GK Linear, as the link between the motor and the pump piston, not only accurately transmits the axial forces, but also compensates for parallel and angular displacements, thus ensuring that the sealing system is relieved of any tensions that may occur.
In accordance with the lifting forces in these pumps, the range includes a total of 5 sizes for maximum axial loads between 800 N and 13,000 N, depending on the coupling size.
The coupling hubs as well as the inner ring of the cardan coupling are made of light aluminium and ensure a low mass of the couplings. This is essential for the dynamic lifting processes of the precision pumps.
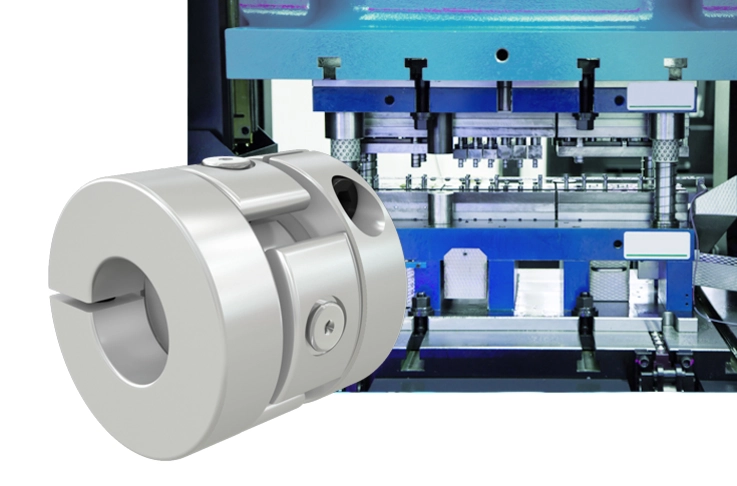
14.06.2023
Test stands are facilities equipped with measuring instruments for testing machines, devices, components or materials for certain properties, in particular functional efficiency, operational safety, behaviour under prolonged load or at high speeds. In order to guarantee the most accurate measurement results as well as exact reproducibility and scalability of test procedures, hardware and software components must be carefully selected so that they enable perfect interaction in the test stand. Our current industry page "Test technology" shows you how different the requirements can be in the most varied test systems and with which properties compensating couplings react as an important integral component in the drive train of test benches.
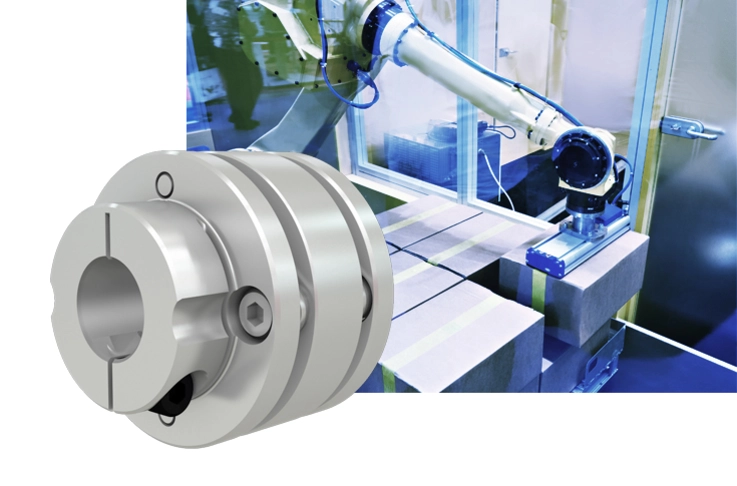
02.06.2023
Torque is of decisive importance in manufacturing processes and in quality assurance. such as the pretensioning of screw connections. Therefore, reliable tools such as torque spanners are indispensable. This torque tool is basically a testing device that is used for the defined and controlled tightening and/or loosening of screw connections. In order for these torque tools to work reliably over a longer period of time, it is necessary to check the setting values after corresponding load changes with subsequent calibration and possible readjustment. This makes the test equipment a permanently reliable tool in the quality-relevant processes.
The Servoflex servo disk coupling ensures optimum interaction for exact measurement results
With test stands designed for these measurements, it is essential that the torque applied by the device under test is applied exactly to the sensor system of the measuring device. The Servoflex servo disk coupling proves to be the ideal partner for this demanding task. Lightweight and with minimised mass inertia, combined with pronounced torsional rigidity and zero backlash - these are the features of the Servoflex and thus guarantee the optimum interaction for achieving exact measurement results. The Servoflex SFC 050D is a double-cardanic version with a torsional stiffness of 16,000 Nm/rad and compensates radial displacements of up to 0.28 mm, axial displacements of up to 0.8 mm and angular displacements of up to 2°. It is available for speeds up to 10,000 min-1.
14 coupling sizes for nominal torques up to 250 Nm
The range offers a wide performance spectrum. The range includes 14 coupling sizes in a nominal torque range from 0.25 to 250 Nm. The coupling is offered in both single-cardanic and double-cardanic versions. The single-cardanic version combines the highest possible torsional stiffness with a very compact design. It enables the compensation of axial and angular shaft misalignments. For multi-axis systems, two single-cardanic couplings offer the ideal combination option for an intermediate shaft coupling for high-precision, synchronised work processes. In addition to the mentioned misalignment possibilities of the single-cardanic version, the double-cardanic version compensates for radial misalignments. Due to its high torsional stiffness, it is the solution in dynamic applications where a high-precision motion sequence in combination with the compensation of universal shaft misalignments is required.
Learn more about the Servoflex

09.05.2023
Whether in laboratory analysis equipment or in pick-and-place systems for the production of electronic components or whether in fluid or micro-metering pumps - when it comes to precise feed tasks in these miniature applications, linear units in miniature format come into their own. As a precision unit, however, they only function accurately if they have the right partner at their side.
The partner for perfect interaction: The Servoflex in miniature format
The Servoflex servo disk coupling in miniature format is the perfect solution for optimum interaction. Light, strong, precise and made for dynamic miniature applications: As a miniature version in an outer diameter range of 12 to 19 mm, the compensating couplings equipped with clamping hubs cover a nominal torque range of 0.25 to 1 Nm and are available for the smallest shaft diameters of 3 to 8 mm. Their torsional stiffness of up to 700 Nm/rad (double cardanic version), depending on the size, underlines the pronounced positioning and repeat accuracy of the linear system. The servo couplings are available as single or double cardanic versions.
Learn more about the Servoflex
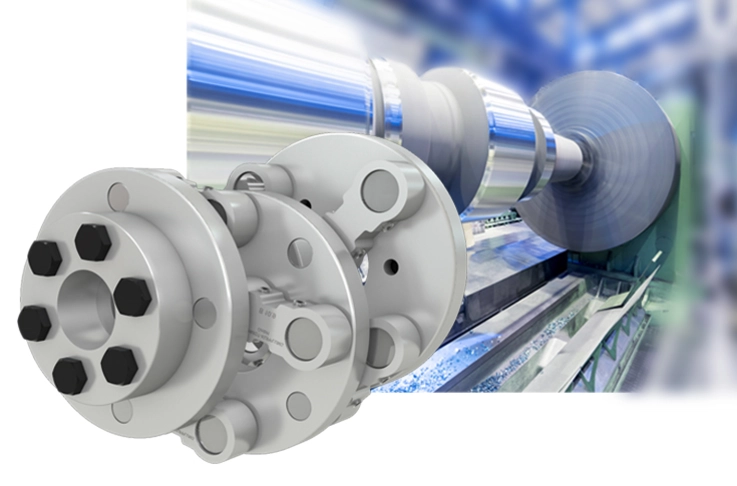
28.04.2023
For an even greater variety of shaft connections, we have currently made the range of our bore diameters for the Semiflex and Schmidt-Kupplung series even more extensive for you. Depending on the coupling size, we offer a range of bore diameters of up to 15 different diameters in the hub design with locking-assemblies (hub version 3).
Discover the new variety? Simply use our configurators and put together your individual precision coupling easily and conveniently.
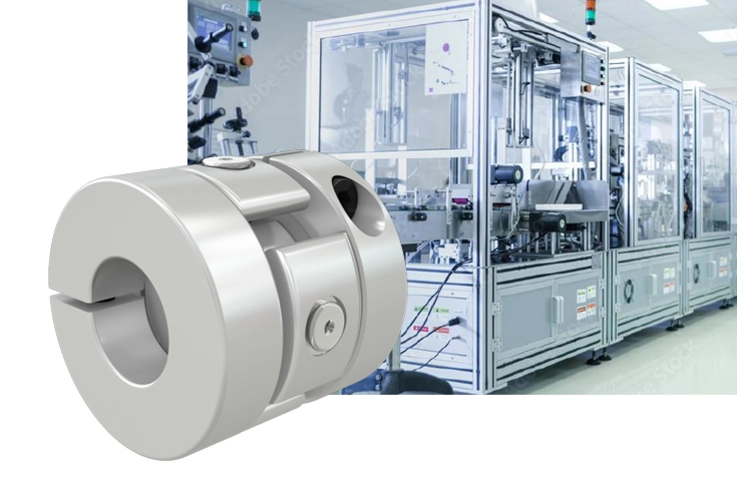
08.03.2023
High temperatures - these are deliberately induced in special systems and are a controlled part of a process, for example to harden manufactured workpieces or to completely remove production residues from prefabricated components or components in the finishing stage in a hot-air drying process.
Adapted for thermal processes: Loewe GK Torque in stainless steel
In the pharmaceutical or food industry, thermal process plants are used at the end of a respective production process for mixing and homogenising, for sterilising and pasteurising or for separating and mixing processes. Adapted coupling designs from the Loewe GK Torque cardan coupling series take over the precise torque transmission here with simultaneous compensation of high parallel and angular misalignments in a compact design.
Stainless steel is used throughout as the material for the couplings. Due to the high ambient temperatures, the axially stiff couplings are additionally equipped with polymer sleeve bearings, which have a high thermal resistance, or with heat-resistant bronze sleeve bearings, depending on the requirement profile.
Demanding lifting process in hardening plant: An easy task for the Loewe GK Linear
The precise transmission of axial forces in hardening plants is handled by the axially stiff couplings from the Loewe GK Linear series.
The load is lifted accordingly via a hydraulic cylinder and a subsequent deflection. The linear coupling has to transmit axial forces of up to 3.000 N due to the design of the length of the stroke-executing axis, the lever of the deflection and the weights of the corresponding workpieces to be lifted.
The coupling is used in the system at higher temperatures. This means that despite the fact that the actual hardening process takes place encapsulated away from the drive, there is an increased thermal condition at the coupling. In addition, it is exposed to an oily atmosphere due to the use of hardening oils. These hardening oils, which are based on mineral oils, are used as a quenching medium for the materials and play a decisive role in the subsequent properties of the metallic workpieces, such as their strength and toughness.
With its compact dimensions, the Loewe GK L in size 56 used for this purpose supports the space-saving design of the system and is able to compensate for radial displacements of up to 2 mm as well as angular displacements of up to 3° resulting from occurring tensions.
Its axial rigidity of 32.000 N/mm ensures the precise transmission of linear lifting forces.
The high-performance plain bearings used in the linear coupling have a high thermal resistance of up to 250° C and show very good resistance to chemicals, e.g. organic solvents, oils, greases, and thus correspond to the environmental conditions mentioned in the system.
Learn more about the Loewe GK

04.02.2023
When it comes to precise measuring tasks in corrosive or special atmospheric ambient conditions - encoders and sensors designed for this need a reliable and coordinated partner as a compensating coupling. You have found this with the new Sensorfit encoder coupling.
The lightweight and modular compensating coupling has innovative clamping hubs made of the high-performance plastic PPS (polyphenylene sulphite) 40% glass-fibre reinforced. This high-temperature resistant thermoplastic polymer is extremely low in outgassing and resistant to various chemicals, cleaning agents and water vapour and at the same time meets the requirements for applications in the food sector. The careful matching of the other coupling components consisting of the functional element made of POM, the chemically nickel-plated locating pins as well as the radially operable, self-locking thermoplastic screws - optionally made of steel with zinc-nickel coating or stainless steel - make the Sensorfit the choice as a precise and displacement-friendly encoder coupling, for example for vacuum, medical technology and pharmaceutical applications or applications under the influence of corrosive media.
Thanks to its modular design, the Sensorfit is extremely versatile and can be freely combined with the most common bore diameters.
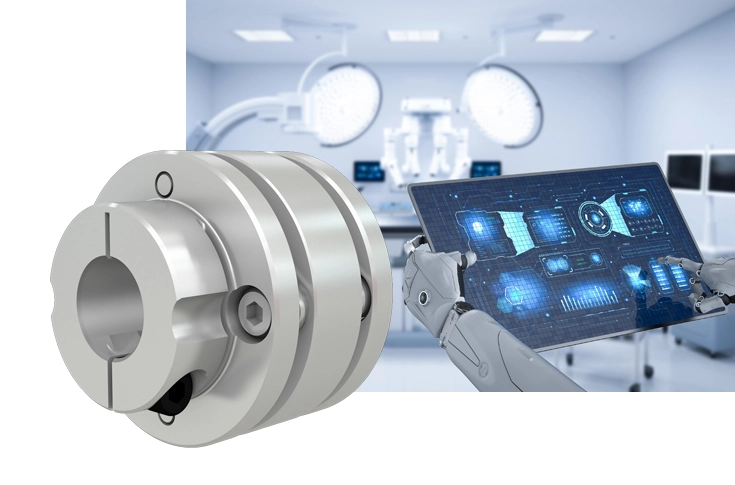
15.12.2022
Backlash-free couplings for modern servo systems are required to fulfil increasingly complex tasks. For machines with optimised cycle times providing ever-increasing output rates, coupling systems are needed which operate with absolute reliability and high precision, in line with the required positioning and repeat accuracy. Furthermore, a low moment of inertia is an essential feature for these dynamic work processes.